Advantages
Designed on basis of hydrodynamics theory, lower motor power, more energy saving.
Optimized rotor and screen basket design makes fiber sufficiently fluidized thus higher screening efficiency.
Module design, stable and reliable structure, saving labor and time for installation and maintenance.
Equipped with automatic oiling device and mechanical sealing water flow detection device, DCS interface reserved (detection of temperature rise and vibration of bearing), high degree of automation.
Structure And Principle
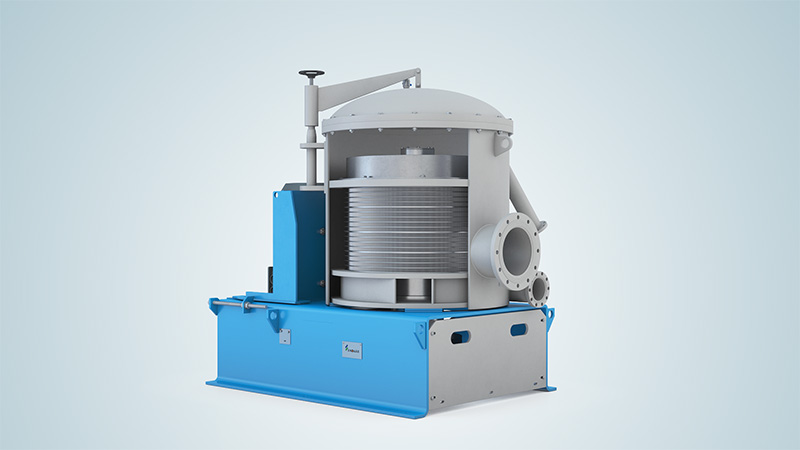
Screening Technology
Operation of pressure screen is based on principle of discharging contaminants through screen, including actual separation and possible separation. Actual separation means the contaminants cannot pass the holes on screen basket irrespective of the orientation of contaminants. The smaller the holes are, the higher actual separation ability of screen. Possible separation means separating by preventing the contaminants to pass the holes by a certain moving orientation of contaminants. Influence factors are discharge rate, consistency, pressure drop, design, temperature and PH value of pulp, rotating parts design, screen basket structure and position of rotor, etc.
Function of screen basket/rotor
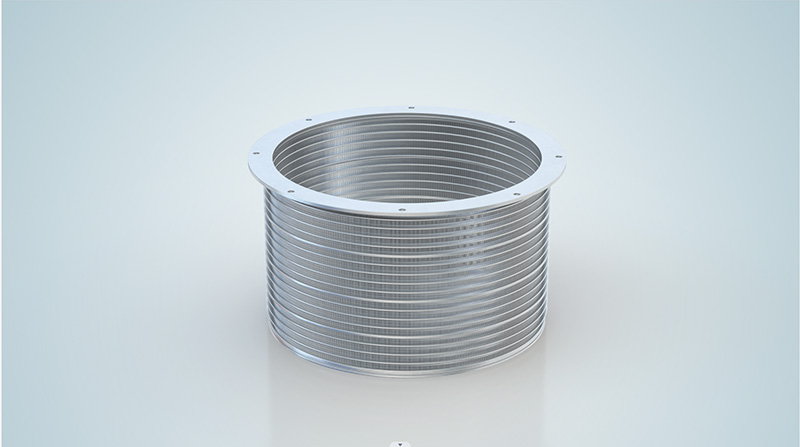
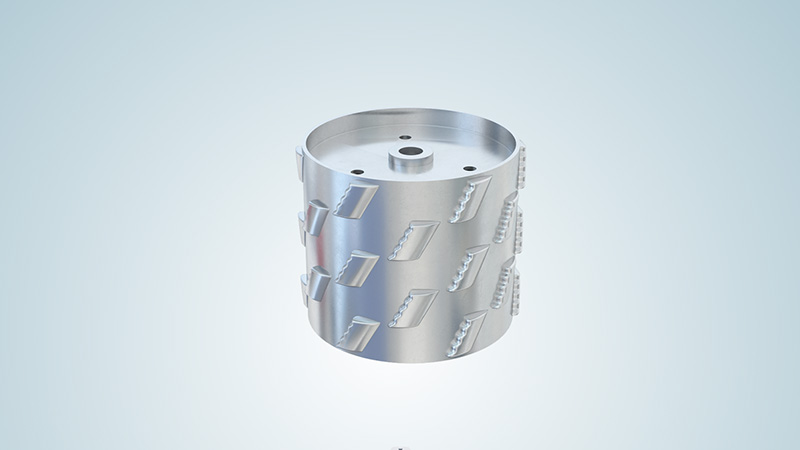
When pulp enters basket from bottom of equipment, a rotor with foils contacts the pulp. The rotor has two functions: firstly, vortex formed by rotor produces mixing effect and forms turbulence on surface of basket; secondly, negative pulse occurs from rotor foils. The turbulence and suction force prevent screen holes from being blocked. Accepted stock will be discharged out from the basket while reject stock and contaminants will be discharged from top of pressure screen. Big and heavy contaminants will be discharged through heavy reject pipe on bottom of screen. Heavy reject pipe should be checked regularly.
Technical Data
Model | SS10 | SS20 | SS30 | SS35 | SS40 | SS45 | SS50 | SS55 | SS60 |
Inlet Dia. (mm) | 150 | 200 | 250 | 300 | 300 | 400 | 400 | 400 | 400 |
Accept Dia. (mm) | 150 | 200 | 250 | 300 | 300 | 400 | 400 | 400 | 400 |
Heavy Reject Dia. (mm) | 80 | 100 | 100 | 125 | 125 | 150 | 150 | 200 | 200 |
Light Reject Dia. (mm) | 80 | 100 | 100 | 125 | 125 | 250 | 250 | 250 | 250 |
Dilution Dia. (mm) | 40 | 50 | 50 | 65 | 65 | 65 | 65 | 80 | 80 |
Nomonal Area (㎡) | 0.38 | 0.62 | 1.07 | 1.51 | 1.80 | 2.36 | 2.80 | 3.39 | 3.96 |
Capacity (T/D) | 40-120 | 80-220 | 120-330 | 180-450 | 210-560 | 270-620 | 330-870 | 390-930 | 450-1100 |
Max.Motor (KW) | 11-22 | 15-37 | 37-45 | 37-55 | 45-75 | 45-90 | 55-110 | 75-132 | 90-160 |
Case
2017 Xinjiang Dongshengxiang Paper Industry.
200,000 tons OCC slurry line coarse screen, grading screen, fine screen,SS series screen.
